- Boshart Knowledge Base
- Chemical Composition
-
Air Volume Controls
-
American Iron and Steel
-
Back Flow Prevention
-
Ball Valves
-
Bleeder Orfice
-
Brass Fittings
-
Bronze Threaded Pipe Fittings
-
Certifications
-
Check Valves
-
Chemical Compatibility
-
Chemical Composition
-
Clamps
-
Compression Coupling
-
Compression Fittings
-
Conflict Minerals
-
Constant Pressure Manifold
-
Control Box
-
CRN
-
Dielectric
-
Drain Back Valve
-
Drain Valves
-
Electrodes
-
Feet of Head
-
Filter Cartridge
-
Filter Housing
-
Filter Housings
-
Filtration
-
Flanges
-
Flare Fittings
-
Float Switch
-
Float Valve
-
Float Valves
-
Flow Controls
-
Foot Valves
-
Gallons
-
Galvanized
-
Gas
-
Gas Connector
-
Gate Valves
-
Gauges
-
Hand Pump
-
Heat Shrink
-
Hose
-
Hose Bibb
-
Hose Fittings
-
Insert Fittings
-
Iron Out
-
Jet Pumps
-
Leathers
-
Level Alarms
-
Literature
-
Malleable Iron Fittings
-
Manifolds
-
Merchant Coupling
-
Merchant Steel
-
Mounting Bracket
-
MTR
-
NPT Threads
-
NSF
-
O-Rings
-
PEX Fittings
-
PEX Valves
-
Pig Tail Syphon
-
Pipe
-
Pipe Column
-
Pipe Fittings
-
Pipe Nipples
-
Pitless
-
Pitless Adapter
-
Pitless Unit
-
Pressure Gauge
-
Pressure Snubber
-
Pressure Switch
-
Pressure Tank
-
PTFE
-
Pump Cable
-
Pump Saver
-
Push-Fit
-
PVC Fittings
-
PVC Pipe
-
Ratings
-
Relay
-
Relief Valves
-
Rope
-
Rope Hanger
-
Safety Data Sheets
-
Sewage Valves
-
Shaft Seals
-
Snifter Valve
-
SPIN-DOWN
-
Stainless Steel
-
Stainless Steel Fittings
-
Steam
-
Stop & Waste Valves
-
Sump Pump
-
Sump Pump Check Valve
-
Sweat
-
Tank Tee
-
Tank Tees
-
Technical Support
-
Thermometer
-
Thread Sealants
-
Torque Arrestor
-
Trouble Shooting
-
Tubing
-
Unit Conversions
-
Vacuum Breaker
-
Wall Hydrant
-
Warranty
-
Water Well Accessories
-
Well Cap
-
Well Caps
-
Well Packers
-
Well Point
-
Well Seal
-
Well Water Systems
-
Wire
-
Wiring
-
WROT
-
Yard Hydrants
-
Electrical Enclosures
-
Transition Couplings
-
Water Box
-
PEX Pipe
-
Combination Valve
-
Well Screen
-
Flowing Well
-
RoHS - Restriction of Hazardous Substances
-
Electrical Tape
What is the Chemical Composition of C46500 Brass Alloy?
The chemical composition of UNS C46500 copper alloy is outlined in the table below (https://alloys.copper.org/alloy/C46500):
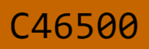
Element |
Content (%) |
Copper, Cu |
59-62 |
Arsenic, As |
0.02-0.06 |
Tin, Sn |
0.50-1.0 |
Lead, Pb |
0.2 |
Iron, Fe |
0.1 |
Zinc, Zn |
Remainder |
Dezincification Resistance
There are materials, such as copper alloys, that have a high copper content (81-86%) and low zinc content (<15%). Copper alloys having less than 15% zinc are considered to be immune to dezincification due to their chemical composition. They are commonly referred to as red brasses or bronze alloys.
However, brass alloys having a zinc content over 15% are yellow brasses. They are the most common material used since yellow brass is less expensive and is produced in high volumes because it preforms well in the majority of plumbing applications. Yellow brasses have a much lower copper content (56-61%) and a significantly higher zinc content (35-37%) so they are susceptible to dezincification.
There are various types of “Dezincification Resistant” (DZR) yellow brasses available. The increased resistance is gained by adding inhibitors such as arsenic, for example. The addition of arsenic allows for the brass to have a higher zinc content. Arsenic, typically in the 0.02 – 0.15% range, will allow a copper alloy to inhibit the selective dissolution of zinc caused by contact with water. DZR brass increases the anti-corrosive properties, but this does not mean they are immune to dezincification entirely.
Brass (yellow brass) is the most widely used copper – zinc alloy in plumbing. In some circumstances, when exposed to certain combinations of pH and concentrations of chlorides, it can experience a severe form of corrosion known as dezincification. This is where the zinc dissolves out of the brass, weakening and compromising the mechanical properties of the alloy.
Although potable water is unlikely to cause dezincification, it is capable! Where distribution systems might introduce water conditions or fluids that may be more prone to cause dezincification, you should use Dezincification Resistant Brass fittings and valves at minimum. However the selection of a more suitable bronze or stainless-steel product may be required to prevent failure due to dezincification.
In heating, ventilation, and air conditioning (HVAC) applications, dezincification can result in system failure by causing leaks, blockages or even ruptures. It is therefore a major consideration when it comes to system design and material selection.
IMPORTANT:
The selection of suitable products and materials is the sole responsibility of the system designer, installer or end user of the product. If unsure, advice can be sought from your local water authority or from a corrosion expert in order to understand if you need to consider specialised components or materials for your project based on local water quality, or soil conditions if the product is installed underground. In some areas due to water and soil conditions the AHJ (authority having jurisdiction) may mandate that valves or fittings be dezincification resistant at minimum. In our opinion it is better to be safe than sorry. The best practice for underground or direct burial, critical applications or hard to access locations is to avoid the use of yellow brass or DZR brasses. The selection of red brass, bronze or stainless steel are superior options for critical and direct burial applications.
Additional Resources:
Copper Development Association Inc.
https://www.copper.org/applications/rodbar/pdf/7013.pdf
AMPP - The Association for Materials Protection and Performance
https://www.ampp.org/technical-research/what-is-corrosion/forms-of-corrosion/dezincification
Corrosion Doctors
https://corrosion-doctors.org/Forms-selective/dezinc-valve.htm