When researching this topic, you will find conflicting information on the effects of joining these dissimilar metals. One thing that becomes clear is that this is a complex topic. I trust the information provided below will be helpful to you in making a decision as to the suitability or risks when joining these metals.
In a blog “What Metals Get Along? What Metals Don’t” written by APP Manufacturing it is stated that “metals like copper and stainless steel are similar. That’s why steel pipes and copper tubing work well together. They are similar enough that they usually don’t need to be insulated from one another.”
https://www.appmfg.com/blog/the-intro-guide-to-dissimilar-metals
Examples Where Brass or Copper and Steel or Stainless Steel Have Been Joined Directly Without Any Notable Issues:
#1 – Brass to Galvanized Pipe: Brass gate and ball valves are commonly joined directly to galvanized pipes.
#2 - All the well-known brands of Frost-Free Yard Hydrants use this combination of dissimilar metals. It is not uncommon for this combination of metals to last 20 – even 50 years even though these materials are very far apart on the galvanic charts, having an anodic difference of 0.850 V. This is way over the acceptable range of 0.15V to 0.25V, covered later in this article.
#3 – Push-Fit fittings use a thin SS gripper that is in direct contact with copper pipe. These fittings will produce condensation (sweat) with cold water flowing through the piping creating an electrolyte. To this point in time, we are not aware of any issues with these dissimilar metals corroding, although in direct contact.
#4 - Submersible pump manufacturers were using SS shells for the wet end of the pump with brass ends for many years. I have never heard of any issues…EVER!
The above are examples you can draw on from your own experience and may help in your decision-making process. NOTE: Boshart has developed a new and improved YHSS series yard hydrant that has a 304SS valve body, standpipe, connecting rod, and coupling to provide a high level of corrosion resistance. This will be a great solution to eliminate galvanic corrosion issues that are sometimes experienced in areas with aggressive soil and water conditions.
Best Practice
Although the risk of galvanic corrosion is minimal, it is always best to avoid joining dissimilar metals directly together whenever possible! The good news is that if you must join brass or copper to stainless steel the galvanic corrosion will be insignificant.
Why do some stainless steel alloys and copper or copper alloy brasses work together while others do not…
Metals being joined directly should have no more than a 0.15V to 0.25V differential on the anodic index. This is typically seen between metals that are extremely close together as listed on the index. In the case of stainless steel (410) and brass, they are seven metals apart, with a difference of 0.250V. This is at the maximum of the limit, and they would be likely to corrode if connected directly. Comparatively, when joining 301, 304 and 310 stainless steels with copper/brass, they are only two metals apart and have a 0.15V difference. This is well within the acceptable range meaning they can be safely connected with minimal risk of galvanic corrosion.
https://www.nuflowmidwest.com/will-using-dissimilar-plumbing-pipe-metals-accelerate-pipe-corrosion/
The Anodic Index copied below is found at the Research Gate site:
https://www.researchgate.net/figure/Anodic-index-of-metals-2_tbl1_288427213
Some galvanic action charts, like the one below, support the information from the Anodic Index described above, and indicate that galvanic action is “insignificant” between stainless steel and copper/brass. https://m.ebrary.net/49865/health/combination_metals_steels_alloys_avoid_bimetallic_corrosion_galvanic_corrosion
Although the risk may be minimal, we cannot say how other factors such as the Ph, oxygen, mineral levels of the water, all combined with fluid temperature will affect the rate of corrosion.
On the Contrary… you will also find galvanic action charts which differ from the one above, indicating that there will be corrosive action, and that the metal combination should not touch and must be insulated.
Three conditions must be met in order for galvanic corrosion to occur...
According to Corrosion Doctors, there are three conditions that must be met in order for galvanic corrosion to occur.
- Two or more dissimilar metals must be located within the system.
- There must be electrical contact between the dissimilar metals.
- An electrolyte must be present. Water, moisture, and humidity can be considered electrolytes under the right conditions.
https://www.corrosion-doctors.org/Books/Handbook.htm
https://www.corrosion-doctors.org/Forms-galvanic/galvanic-corrosion.htm
How to Prevent Galvanic Corrosion
- Never use dissimilar metals when installing the plumbing system, including fasteners, hangers, bolts, screws, etc. Even a screw in a dissimilar metal can cause accelerated corrosion around the screw.
- Minimize the risk of galvanic corrosion by only using similar metals within the plumbing system and double-check that they are similar by referencing the anodic index.
- If dissimilar metals must be used within a plumbing system, connect the two pipes with dielectric connections or a non-metallic barrier. This will prevent electrical contact between the two dissimilar metals.
Practical Solutions:
At any rate, regardless of the conflicting information, and that the risk of galvanic corrosion is minimal, we suggest you consider one of the following 4 options below when transitioning from copper or brass to 304 S.S. whenever it is possible.
#1 - Install a non-metallic bushing or pipe nipple as a barrier between the copper or brass component and the SS PEX fitting. NOTE: This may not always be viable depending on the fluid temperature. PVC bushings or pipe nipples for example, are not suitable for high temperature applications. CPVC thermoplastics can handle fluids at service temperatures up to 200°F, allowing a wide range of process applications, including hot corrosive liquids.
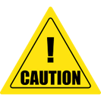
CAUTION: P.T.F.E. thread seal tape used on an NPT joint is not designed to be an isolator and is not considered to be a reliable barrier or means of galvanic isolation. You will find articles that say PTFE is a galvanic barrier and this is true for some applications, however it does not apply to NPT pipe thread connections. The threads simply cut through the PTFE tape. PTFE tape allows the two pieces to turn easily until they do reach the point of metal-to-metal contact which eliminates any barrier.
#2 – Install polysulfone PEX fittings (Series 710 P (Crimp) or 710CEP (CEP)) directly into the copper or brass component to avoid galvanic corrosion. Then you can use the 304SS PEX fittings downstream. The PEX pipe will function as the non-metallic barrier.
https://boshart.com/product-category/master/fittings/pex_fittings/poly_pexfittings_fittings/
#3 – Consider sourcing or using a stainless steel component such as a valve, manifold, water meter, circulator pump etc. when you plan to use 304 SS PEX fittings. Stainless steel plumbing devices continue to grow in popularity and are becoming more readily available, reducing the need to join dissimilar metals.
#4 – Consider installing copper or brass PEX fittings directly into the copper or brass component, then switch to 304SS PEX fittings downstream.
NOTE: Option 1, using a non-metallic barrier, and Option 2, using a polysulfone PEX fitting, are superior options over brass PEX fittings in our opinion. Why? Brass is susceptible to dezincification, and this combined with the thin wall thickness of a PEX barb can result in leakage over time. Dezincification selectively removes zinc from the brass alloy, leaving behind a porous, copper-rich structure that has little mechanical strength. An in-service brass fitting valve suffering from dezincification will have a white powdery substance or mineral stain on its surface. The fitting may exhibit water weeping through the cast body. Zinc is the least noble metal on the galvanic chart and Boshart offers 304SS PEX fittings instead of brass PEX fittings for this reason.
At the end of the day, the end user, system designer or authority having jurisdiction over the project will have to make the decision after carefully evaluating all the factors and potential risks of cost and water damage that could occur in the event of failure due to galvanic corrosion. Boshart is not a corrosion expert and encourages you to do your own research on this complex subject to validate the information we have provided. Reaching out to a corrosion expert for further advice on your application is recommended.
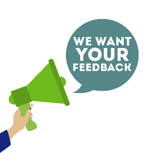
Boshart will continue to do research on this topic and will update this article when we find information that warrants a change to the advice provided. We are always looking for feedback whether it be additional articles or resources on this topic or even what you have experienced in the field with regards to the effects of joining 304 SS with either copper or brass components.
Additional Resources:
https://www.copper.org/applications/plumbing/techcorner/pdf/galvanic_corrosion.pdf
https://www.phcppros.com/articles/2867-corrosion-plumbing-piping
https://www.ssina.com/education/corrosion/galvanic-corrosion/
https://www.worldstainless.org/Files/issf/non-image-files/PDF/Euro_Inox/Contact_with_Other_EN.pdf
https://www.ampp.org/technical-research/what-is-corrosion/forms-of-corrosion/dezincification
https://www.corrosionpedia.com/definition/384/dezincification