- Boshart Knowledge Base
- Flanges
-
Air Volume Controls
-
American Iron and Steel
-
Back Flow Prevention
-
Ball Valves
-
Bleeder Orfice
-
Brass Fittings
-
Bronze Threaded Pipe Fittings
-
Certifications
-
Check Valves
-
Chemical Compatibility
-
Chemical Composition
-
Clamps
-
Compression Coupling
-
Compression Fittings
-
Conflict Minerals
-
Constant Pressure Manifold
-
Control Box
-
CRN
-
Dielectric
-
Drain Back Valve
-
Drain Valves
-
Electrodes
-
Feet of Head
-
Filter Cartridge
-
Filter Housing
-
Filter Housings
-
Filtration
-
Flanges
-
Flare Fittings
-
Float Switch
-
Float Valve
-
Float Valves
-
Flow Controls
-
Foot Valves
-
Gallons
-
Galvanized
-
Gas
-
Gas Connector
-
Gate Valves
-
Gauges
-
Hand Pump
-
Heat Shrink
-
Hose
-
Hose Bibb
-
Hose Fittings
-
Insert Fittings
-
Iron Out
-
Jet Pumps
-
Leathers
-
Level Alarms
-
Literature
-
Malleable Iron Fittings
-
Manifolds
-
Merchant Coupling
-
Merchant Steel
-
Mounting Bracket
-
MTR
-
NPT Threads
-
NSF
-
O-Rings
-
PEX Fittings
-
PEX Valves
-
Pig Tail Syphon
-
Pipe
-
Pipe Column
-
Pipe Fittings
-
Pipe Nipples
-
Pitless
-
Pitless Adapter
-
Pitless Unit
-
Pressure Gauge
-
Pressure Snubber
-
Pressure Switch
-
Pressure Tank
-
PTFE
-
Pump Cable
-
Pump Saver
-
Push-Fit
-
PVC Fittings
-
PVC Pipe
-
Ratings
-
Relay
-
Relief Valves
-
Rope
-
Rope Hanger
-
Safety Data Sheets
-
Sewage Valves
-
Shaft Seals
-
Snifter Valve
-
SPIN-DOWN
-
Stainless Steel
-
Stainless Steel Fittings
-
Steam
-
Stop & Waste Valves
-
Sump Pump
-
Sump Pump Check Valve
-
Sweat
-
Tank Tee
-
Tank Tees
-
Technical Support
-
Thermometer
-
Thread Sealants
-
Torque Arrestor
-
Trouble Shooting
-
Tubing
-
Unit Conversions
-
Vacuum Breaker
-
Wall Hydrant
-
Warranty
-
Water Well Accessories
-
Well Cap
-
Well Caps
-
Well Packers
-
Well Point
-
Well Seal
-
Well Water Systems
-
Wire
-
Wiring
-
WROT
-
Yard Hydrants
-
Electrical Enclosures
-
Transition Couplings
-
Water Box
-
PEX Pipe
-
Combination Valve
-
Well Screen
-
Flowing Well
-
RoHS - Restriction of Hazardous Substances
-
Electrical Tape
How to Install a Gasket and Flange
Step #1:
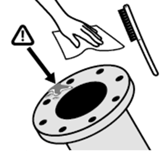
Prior to installation visually inspect and clean flanges, ensuring they are free from all dirt and debris.
Step #2:
Lubricate the bolts, nuts, and nut bearing surface.
Step #3:
Install the new gasket, bolts, and nuts. Hand tighten the nuts and check to make sure the gasket is center. Note: never reuse an old gasket or install multiple gaskets.
Step #4:
Number the bolts in a cross pattern sequence as per the diagram below.
Step #5:
Starting with bolt 1 and following the sequence, snug the bolts up to 10-20 ft/lbs torque (20% of the final torque) and check the gap for uniformity.
Step #6:
Proceed to tighten the bolts in sequence rounds to the following percent of final torque:
4-8 Bolt Pattern: Round 1 = 30%, Round 2 = 60%, Round 3 = 100%
12 Bolt Pattern: Round 1 = 20%, Round 2 = 40%, Round 3 = 80%, Round 4 = 100%
Step #7:
Check the gap around the flange between each round for uniform tightening, measured at every other bolt. If the gap is not uniform, adjust by tightening selective bolts until corrected.
Step #8:
After 100% of torque has been reached, make on clockwise rotational round of tightening starting at bolt 1 until no further nut rotation occurs at 100% of the final torque.
Step #9:
Important Re-Torque: After 24 hours repeat round 3 or 4 followed by a rotational round to ensure proper torque is reached.
Additional Resources: